Już od pradziejów ludzie wykorzystywali płyny, aby ułatwić sobie codzienne życie. Najwcześniejsze zapiski wskazują na użycie takich urządzeń jak pompy czy koła wodne do generowania mechanicznej mocy.
Zastosowania sił płynnych obejmują wszelkie sytuacje, w których ciecze lub gazy służą do przenoszenia mocy w formie pracy mechanicznej, ciśnienia czy objętości w systemie. W skład tych systemów wchodzą pompy i sprężarki, które przenoszą określone ilości i ciśnienia cieczy lub gazów w zamkniętych układach. Systemy te mogą mieć różny stopień skomplikowania – od prostych pomp odśrodkowych:
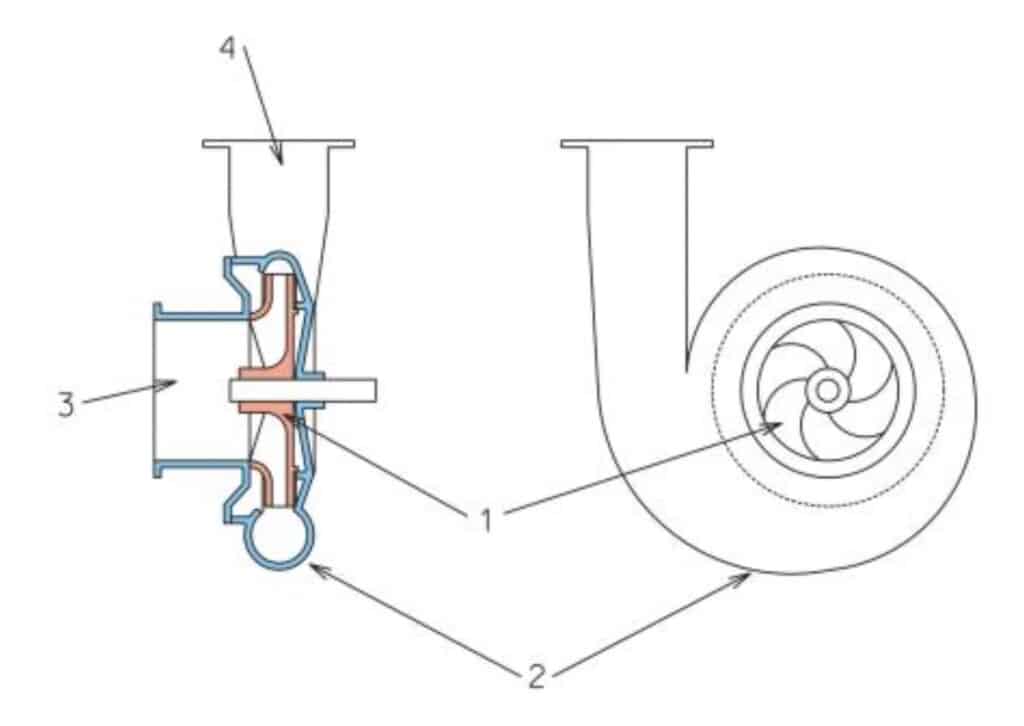
do skomplikowanych układów hydraulicznych używanych w sterowaniu samolotami:
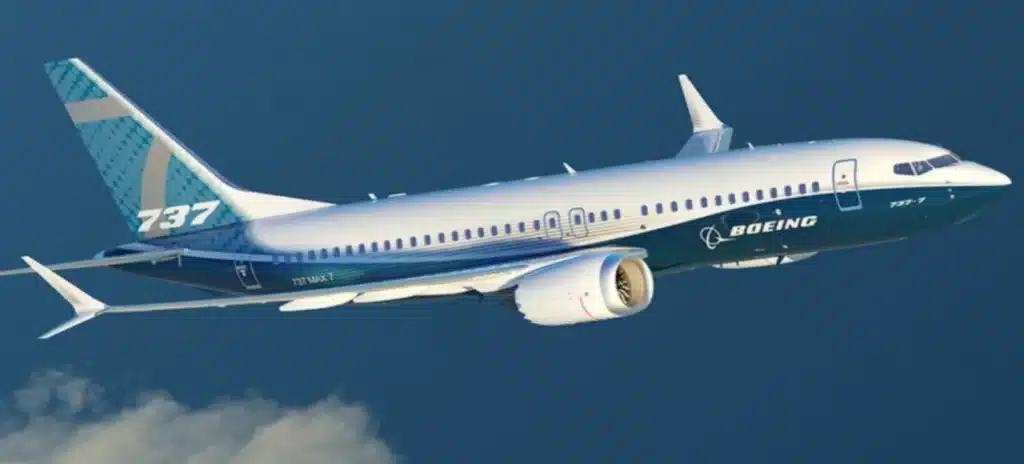
W ciągu ostatnich trzydziestu pięciu lat systemy napędów płynnych rozwijały się dynamicznie. Podczas II wojny światowej napędy płynne odpowiadały na potrzeby zautomatyzowanych maszyn, umożliwiając przesył energii z wykorzystaniem siły mięśni. Dziś technologie te znajdują zastosowanie w wielu dziedzinach życia, takich jak produkcja, transport, ochrona środowiska czy przetwórstwo żywności. Zastosowanie sił płynnych jest praktycznie nieograniczone i zależy od kreatywności.
Istnieją alternatywy dla układów hydraulicznych. Każdy typ układu ma swoje unikalne zalety i wady oraz specyficzne zastosowania, w których sprawdza się najlepiej. Dlatego nie stosuje się układów hydraulicznych w zegarkach czy w przewodach energetycznych.
Zalety hydrauliki obejmują płynne i elastyczne działanie, brak wibracji i odporność na zmiany obciążenia, przy czym w razie przeciążenia układ automatycznie reguluje ciśnienie. Układy hydrauliczne mogą realizować różne ruchy obrotowe i liniowe oraz minimalizować potrzebę ręcznego sterowania, a przy tym są ekonomiczne w eksploatacji.
Hydraulika, pneumatyka i hydro-pneumatyka to trzy podstawowe typy sił płynnych. Wybór odpowiedniego systemu zależy od wielu czynników, takich jak wymagane ciśnienie, precyzja czy kontrola ruchu. Systemy pneumatyczne są tańsze w produkcji i eksploatacji, ale ich zastosowanie jest ograniczone przez ściśliwość powietrza, co wpływa na ich działanie pod obciążeniem. Dlatego systemy pneumatyczne są używane tam, gdzie wymagane są niskie lub średnie ciśnienia oraz precyzyjna kontrola.
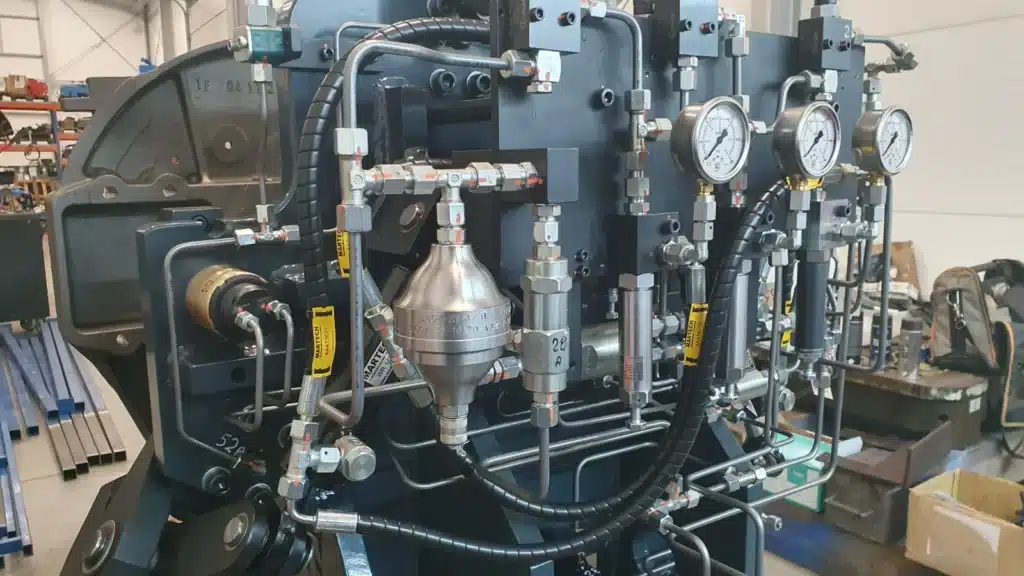
Układy hydrauliczne są bardziej odpowiednie w przypadku wysokiego ciśnienia i dokładnej kontroli. Elastyczność tych systemów wymaga jednak starannego zabezpieczenia przed wyciekami, co jest kluczowe dla zapewnienia bezpieczeństwa i efektywności.
W porównaniu z układami mechanicznymi, hydrauliczne często oferują prostsze i bardziej niezawodne przesyłanie energii dzięki mniejszej liczbie ruchomych części. Systemy te są bardziej efektywne i pozwalają na elastyczne rozmieszczanie komponentów, eliminując potrzebę przekładni czy krzywek.
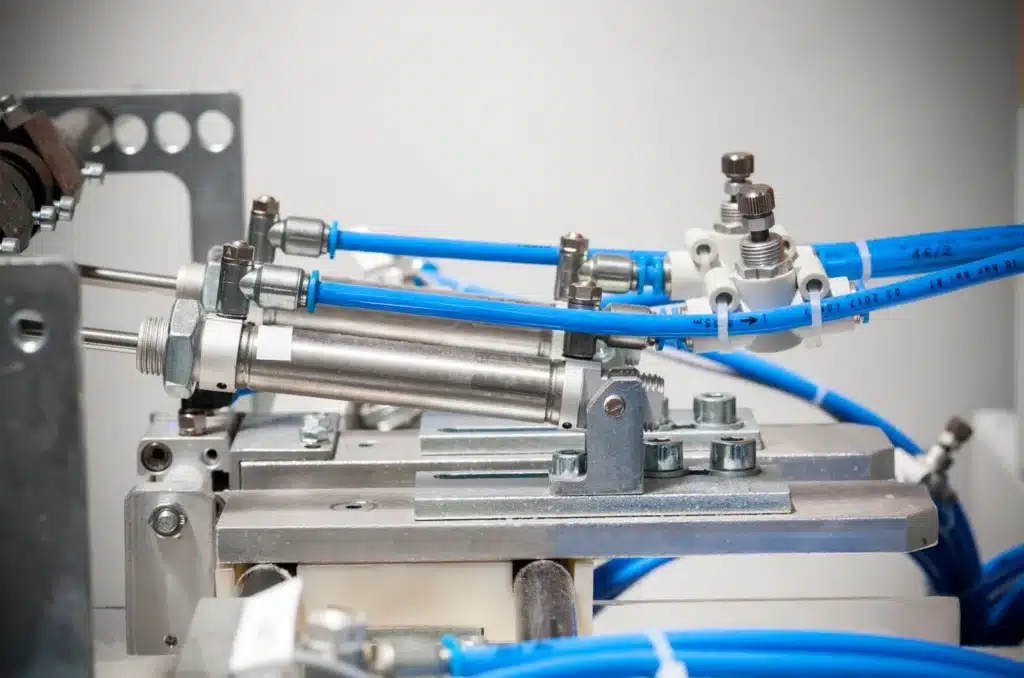
W przypadku porównania hydrauliki z układami elektrycznymi, hydraulika często oferuje prostsze sterowanie prędkością, kierunkiem i siłą dzięki niewielkiej liczbie komponentów, co zwiększa niezawodność i redukuje rozmiar systemu. Problemy specjalne związane z układami hydraulicznymi obejmują tarcie wewnętrzne, które może prowadzić do utraty wydajności lub uszkodzeń, oraz możliwość zatykania małych przejść przez ciała obce.
Ważne jest, aby zapewnić odpowiednią konserwację i znajomość działania układu, aby unikać problemów związanych z korozją i innymi uszkodzeniami. Termin „hydraulika” pochodzi od greckiego słowa oznaczającego wodę, początkowo używaną do przenoszenia mocy. Obecnie hydraulika obejmuje zachowanie wszystkich cieczy, choć głównie koncentruje się na ruchu cieczy.
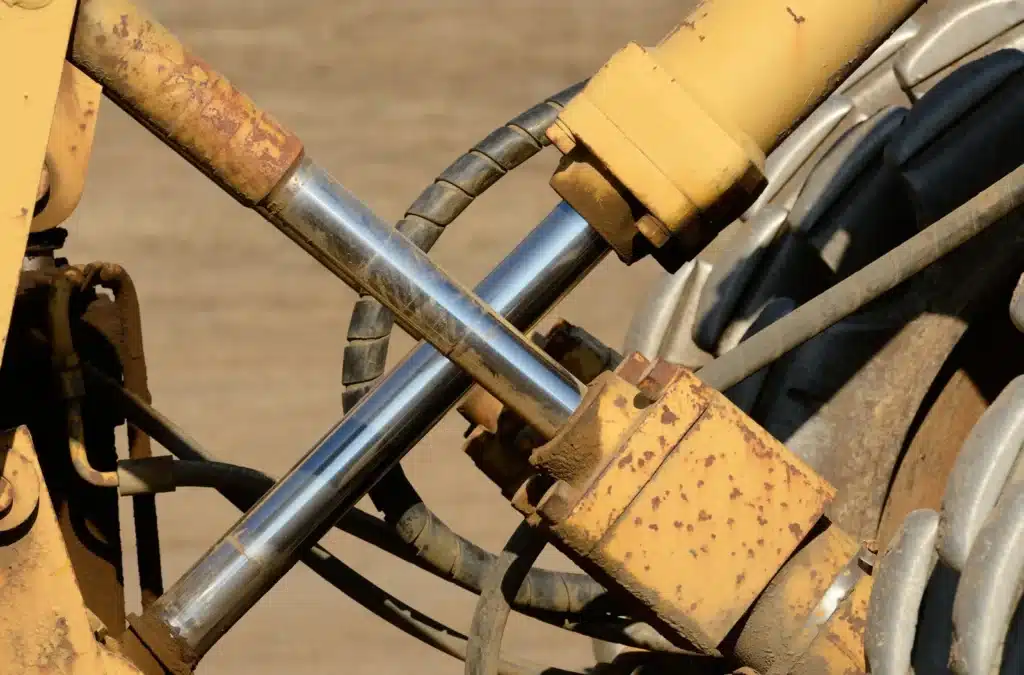
Użycie medium pod ciśnieniem, takim jak płyn hydrauliczny, wiąże się z ryzykiem. W przypadku oleju w wysokociśnieniowych układach hydraulicznych istnieje ryzyko pożaru lub wybuchu, zwłaszcza przy pęknięciu rur i wyparowaniu oleju. W takich przypadkach należy zachować szczególną ostrożność i stosować plan konserwacji zapobiegawczej, aby minimalizować ryzyko.